组合机床是由具有一定功能的通用部件(动力箱、滑台、支承件、运输部件等)和专用部件(夹具、主轴箱)组成的高效率专用机床。加工范围广,自动化程度高,在机械制造业的成批和大量生产中得到了广泛的应用。
动力箱安装在滑台上,动力箱上的电动机带动刀具实现刀具的主运动,滑台用来完成刀具的走刀运动。多数滑台采用液压驱动,以便实现多种进给(快进、一次工进、二次工进和快退等)。多种进给可根据工艺要求安排在一个工序中,也可以用多个滑台同时进行加工。
(1)液压系统的工作原理
图1是一个组合机床液压系统。在本系统中由一台液压泵向多个液压缸供油,因此液压系统必须满足工位之间不干涉的要求,并力求功率损失最小。
在图1中,液压缸7,液压缸13和液压缸17分别控制三个滑台。液压缸14为夹紧缸,液压缸15为输送工件液压缸,液压缸l6为定位缸。由三位四通或二位四通换向阀分别控制各液压缸的往复运动。在油路中可以不接人调速阀,可以接入一个调速阀(如液压缸13,液压缸17的油路),也可接人两个串联的调速阀(如液压缸7、液压缸15的油路),用这种方法使液压缸7、液压缸13、液压缸17进行速度换接完成快进、工进I和工进Ⅱ等动作,同时还可使液压缸15在每个方向上完成常速和缓冲的速度换接。
若三个滑台同时快进,则需要较大流骨,此时液压泵18和蓄能器19联合向三个滑台供油。来自液压泵的油经调速阀3,来自蓄能器的油经阀1和阀2,二者汇合后经阀4进入液压缸7。
在同一时刻有的滑台快进,有的滑台工进时,系统应保证二者不发生干扰。例如,液压缸13、液压缸17的滑台处于快进而液压缸7的滑台处于工进时,行程阀5、6右位,此时阀8、阀9接人系统,调速阀3到阀4这段管路压力升高,单向阀2关闭,蓄能器不再继续向液压缸7供油,进入液压缸7的只有来自液压泵的高压油,液压缸7工进。同时,因液压缸7进油路的压力增高使顺序背压阀10动作,液压缸7回油路中产生背压。此时,液压缸7进行慢速工进,而其他两个滑台仍由液压泵和蓄能器联合供油进行快进,二者互不影响。
若三个滑台液压缸均处于工进状态,来自液压泵的油经顺序阀11向蓄能器充液。当充油压力达到一定值时,溢流阀12开启溢流。
(2)组合机床液压系统的特点
1)本系统采用单泵集中控制,系统对流量的需求量变化较大,采用蓄能器增速回路,可减少系统的功率损失和发热。
2)本系统采用进口节流加背压的调速方法。顺序背压阀在快进时只形成很小的背压,功率损失小;工进时该阀能自动使背压加大,进给速度平稳。
本组合机床的液搓系统和电气系统配合,可自动完成除装卸工件外的全部动作,系统的功率消耗可减少40%。
拉床液压系统
拉削的主运动是由传动系统带动拉刀对工件进行直线切削的运动。它要求输出力大(25~100OkN),调速范围宽(0.02~0.6m/s),并要求无级调速。凼此拉床100%的采用液压传动。图4.18-2是高速立式外拉床液压系统。本系统的最大流量Q= 1000 L/min,最大功率P=11OkW。因此,减少功率损失和系统发热极为重要。本机床除工件装卸需要人工外,其余动作可以自动进行。液压系统丁作原理如下:
(1)送进和锁紧回路
被拉削的工件装在工作台上后,由进给液压缸20将工作台送进到一定位置,然后由液压缸21将工作台锁紧。主液压缸16带动拉刀进行切削。拉削完毕后工作台被液压缸21松开,再由液压缸20将工作台退回原位,然后拉刀靠主液压缸16完成返回行程。各动作的顺序靠各行程开关或压力继电器发出的电信号控制各电磁阀完成。进给液压缸20的进退由定位式二位四通电磁换向阀28控制。锁紧液压缸21由定位式二位四通电磁换向阀29控制。进给系统和夹紧系统共刚一个液压泵27。
(2)液压泵1的变量回路
变量机构由电液比例换向阀8、控制液压缸7、双向作用弹簧阻尼器19、伺服阀9和液压缸10、11组成。电液比例换向阀8由电液比例双向减压阀和电液比例双向节流阀组成。液体经过电液比例减压阀后被减压。减压后的压力值与输入电流大小成正比,不随进口的压力变化。输入的电流可以通过电位器调节。当比例电磁铁30通电后,电液比例换向阀8减压后的压力值决定于电位器电阻的调定值,减压后的压力油流人控制液压缸7上腔。液压缸7的活塞杆一端与伺服阀阀芯相连。另一端与双作用弹簧阻尼器的心轴相连。当液压缸7上腔活塞面积上受到的液压力大于预压紧力时,活塞杆带动伺服阀9的阀芯向下移动,其位移和活塞上的作用力成正比。当作用力与弹簧力平衡时,活塞杆与阀芯均停止运动。伺服阀的阀芯向下移动时与阀体形成开口,压力油经过开口流人液压缸10上腔,推动液压缸10活塞连同阀体一起向下移动。阀体是反馈件,它可将输出量反馈回输入端与输出量比较,从而构成闭环系统。阀体向下移动的结果使伺服阀的开口量逐渐减小乃至为零。这样,液压缸10的活塞即跟随伺服阀的阀芯移动。同时液压缸10的活塞带动液压泵l的定子,活塞的位移使液压泵l的定子和转子形成一定偏心量。偏心量的大小取决于电位器电阻的调定值。因此,调节电位器电阻值的大小,即可改变偏心量的大小,从而改变液压泵1排量。变量机构反向运动时,原理和上述相同,液压泵l的排量得到反向调节。
.jpg)
图1组合机床液压系统原理图
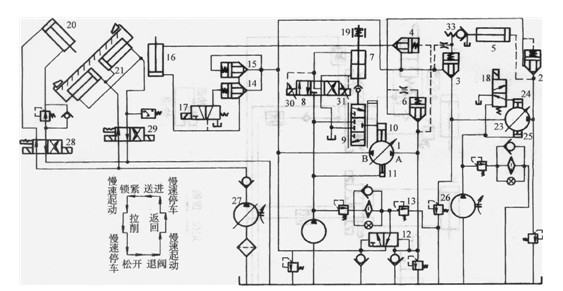
图2拉床液压系统原理图
(3)低速拉削
液压泵23处于零位卸荷,插装阀2、3处于关闭状态,液压泵23不向系统供油,液压泵1的A口为排油口,插装阀4关闭,压力油经插装阀6进入主液压缸16有杆腔,推动活塞,进行低速拉削。无杆腔回袖经插装阀15流人液压泵1的吸油口B。多余的油经梭阀12、背压阀13回油箱。
(4)高速拉削
高速拉削需要大流量,此时液压泵23和液压泵1同时向系统供油。阀18上位工作,液压缸24上腔通压力油。因液压缸24比液压缸25有效面积大,两液压缸中压力相等,故液压缸24活塞上的作用力大于液压缸25括塞上的作用力而推动液压泵23的定子,使之与转子产生偏心。液压泵23排出的油经插装阀2和液压泵1A口汇合后进人液压缸16的有杆腔。此时,液压缸5在压力油作用下顶开单向阀33,使阀3的弹簧腔与油箱相连处于低压状态,阀3开启。液压缸16的活塞下行进行快速拉削。无杆腔的油因阀17通电,左位工作而流过阀14,然后一路经阀3到液压泵23的吸油口或经阀26回油箱;另一路到液压泵1的吸袖口B或经阀12、阀13回油箱。
(5)拉刀快速返回
此时液压泵l的油口B为排油口。比例电磁铁31通电,阀4开启,来自液压泵1的油经阀14进入液压缸16的无杆腔。有杆腔的油经阀4、阀15又回到液压缸16无杆腔形成差动联接。液压缸16活塞快速返回。
液压系统的特点:
l)系统采用插装阀、双向变量泵的闭式油路。具有结构紧凑,换向冲击小、功率损失小等优点,同时也提高了系统的动态性能和通用化程度。
2)高速拉削时经阀14卸荷可减少发热,减少功率损失。
3)泵变量机构用电液比例阀控制可以方便地获得无级调速和远距离控制。
本文标题:
液压系统在机床上的应用(一)
分类:
液压行业知识
标签:
液压系统